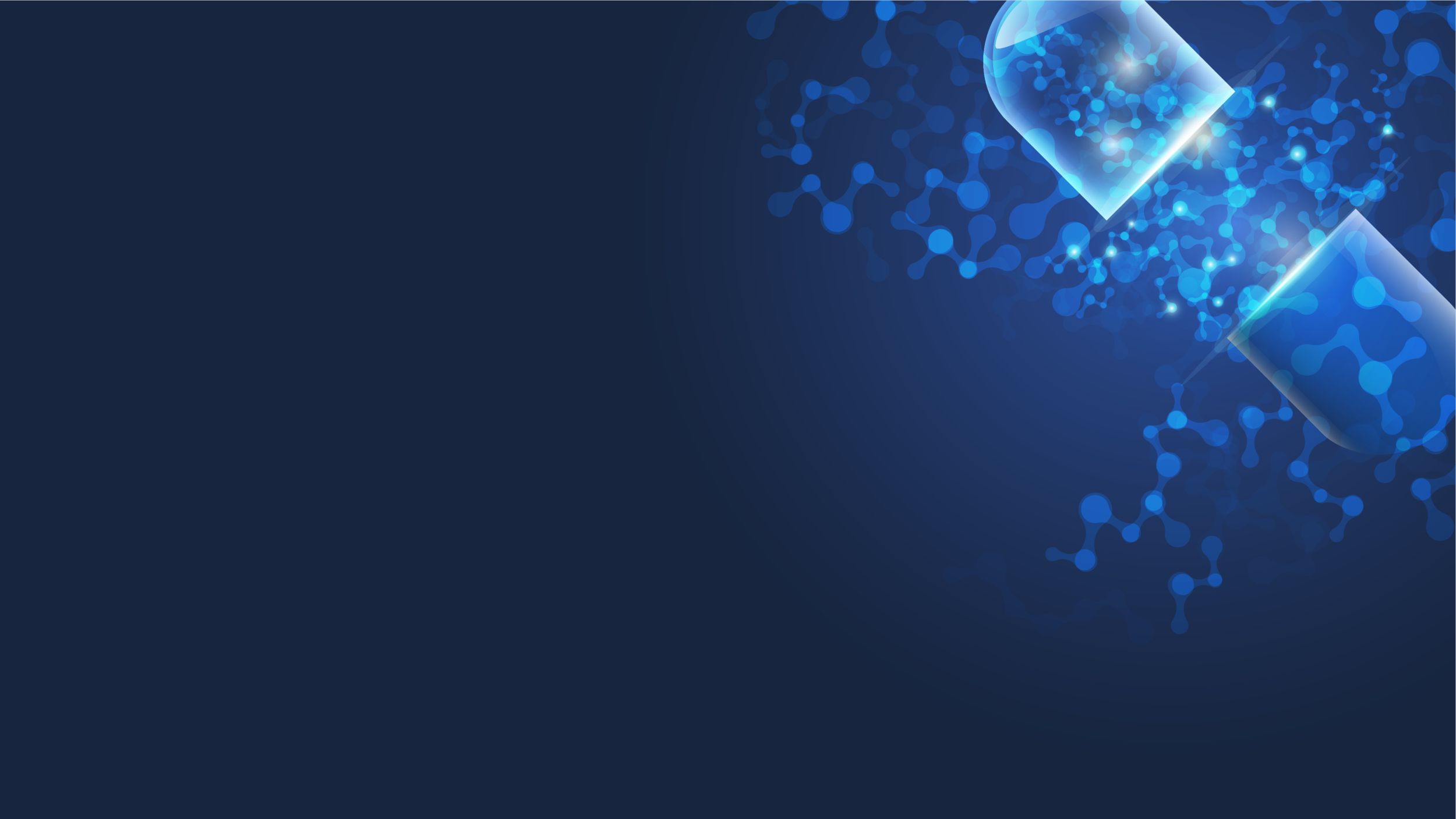
About
CMAC’s Future Continuous Manufacturing and Advanced Crystallisation Research Hub was a seven-year flagship research programme funded by the Engineering and Physical Sciences Research Council (EPSRC) between 2017-2024. It was designed to develop a collaborative, open innovation network for the medicines manufacturing research community to help address major challenges in high-value manufacturing, including the personalisation of medicines to patients.
The Hub was operated in collaboration with CMAC at the University of Strathclyde, University of Bath, University of Cambridge, Imperial College London, University of Leeds, Loughborough University, and University of Sheffield, and supported by CMAC’s Tier 1 and Tier 2 industry partners.
The research undertaken as part of the Hub underpinned the overarching CMAC research portfolio, acting as a National Centre for the medicines manufacturing research community with a focus on research at TRL 2-5.
EPSRC grant reference: EP/P006965/1
Hub vision
Quality by Digital Design
CMAC’s Quality by Digital Design (QbDD) framework advances the Food and Drug Administration’s (FDA) Quality by Design (QbD) approach by integrating modelling and digital tools to drive sustainable, efficient, and innovative pharmaceutical manufacturing. During our research, we applied the framework to three API processes and as a result, QbDD delivered up to 65% material savings and reduced experiments by 28% through digital optimisation. Our 2023 study showcased a digital-first approach to designing mefenamic acid production, enhancing process robustness and flexibility, speeding up medicine development.
Using Quality by Digital Design to accelerate medicines development
Find out more
Transforming pharmaceutical manufacturing with QbDD
Find out more
Digital tools for quality attributes and process design
Find out more
Crystallisation Classification Systems
Developed with Tier 1 partners, the crystallisation classification systems (CCS) user requirements specifications (URS) defines key capabilities of CMAC’s predictive digital framework for chemistry, manufacturing and controls (CMC) development. It integrates models, experiments, and workflows to accelerate medicine development. The URS highlights CCS’s value, technical deliverables, prediction accuracy, and data needs, guiding current and future research beyond CMAC.
A Crystallisation Classification System to accelerate sustainable medicines development
Find out more
CCS publications
Crystallisation Screening DataFactory
The CSDF is an autonomous robotic platform for crystallisation process optimisation. Using QbDD and CCS URS guidance, it combines cobots, automated dosing, and machine learning-driven experimentation. Developed in Phase II, it ensures FAIR data collection, with key datasets stored for future use. Expansion continues through the RPIF Round 7 Data Lab award.
Integrated Supply System Design
This is part of the integrated supply-system design analysis for multi-New Chemical Entity /Active Pharmaceutical Ingredient processes across the crystallisation, isolation and drug product objectives in the Quality by Digital Design Approach to End-to-end Process Design and Operation theme.
Model Driven MicroFactories
As we are using the QbDD Workflow to drive our project, process designs will be established from data collected as a result of following the QbDD Workflows, and then modelled, analysed and optimised to establish a Digital Twin for an Active Pharmaceutical Ingredient or Drug Product manufacturing process, that will inform MicroFactory optimal operating ranges and control strategy. Also, data will be generated to inform the Integrated Supply System Design theme.
For Hub Active Pharmaceutical Ingredient MicroFactories, the default equipment we will use will be MSMPR with integrated PAT-enabled closed-loop control of Critical Quality Attributes linked to continuous or semi-continuous filtration and washing stages and batch drying.
The Drug Product MicroFactory manufacture will be done via polymer processing using extrusion-printing technologies to exploit existing infrastructure across the Hub partners, and alternatively by making capsules.
Hub Research Outputs
Supply Chain
Supply chain workflow aligned with Quality by Digital Design (QbDD) workflow
Papers on investment in digital infrastructure and manufacturing capabilities to enable supply resilience: https://doi.org/10.1111/poms.13865 , https://doi.org/10.1080/01605682.2022.2039565
Quality by Digital Design (QbDD)
BPMN 2.0 mapping version 1.0 of QbDD Workflow complete
Automation of some steps in workflow underway
QbDD strategy paper in preparation
Case studies of how to use workflow to do digital design of API processes in progess
Digital Twins
Lovastatin primary and secondary process MicroFactory models and visualisation
Android App of mefenamic acid MicroFactory Digital Twin
Presentations and paper on gPROMs models for continuous filtration and washing, solvent screening and continuous crystallisation and wet milling: https://doi.org/10.1021/acs.oprd.2c00165
Solubility prediction tools developed further. Includes: A unified AI framework for solubility prediction across organic solvents, https://doi.org/10.1039/d2dd00024e
Easymax training on VR and tablet developed
Hot Melt Extruder VR and 2D graphics
DataFactory Platform
System integration of autonomous crystallisation DataFactory underway
Communication: Autonomous DataFactory: High throughput screening for large -scale data collection to inform medicine manufacture doi: https://doi.org/10.5920/bjpharm.1128
MicroFactories
Modular API MicroFactory assembled and upgrades implemented
Case studies of using QbDD to digitally design processes to make 3 APIs underway. Includes a Tier1 donated API.
Digital design of mefenamic acid API process published: https://doi.org/10.1016/j.cherd.2023.07.003
Tuning shape and size of mefenamic acid crystals using wet-milling and sonication aided Direct Nucleation Control: https://doi.org/10.3390/IOCC_2022-12165
Paper on filtration and washing published: https://doi.org/10.1021/acs.oprd.1c00272
Novel combined Hot Melt Extruder and 3DPrinter secondary processing unit developed and patent applied for
Impact of formulation composition on processing parameters, product properties and performance in secondary processing MicroFactory: https://doi.org/10.1016/j.ijpharm.2022.121505
Advanced Characterisation
CrystalGrowthTracker: A Python package to analyse crystal face advancement rates from time lapse synchrotron radiography https://doi.org/10.21105/joss.04333
Determination of H-atom Positions in Organic Crystal Structures by NEXAFS Combined with Density Functional Theory: A Study of Two-Component Systems Containing Isonicotinamide https://doi.org/10.1021/acs.jpca.2c00439
Drug Product Performance Model Development
Development of swelling-driven OSD dispersion model
Experimental validation method developed for swelling of individual granules/tablets
Papers on mechanistic study of single granule disintegration behavior and a new mathematical model for swelling driven granule disintegration mechanisms planned